product > Panels for OEM users
Following are the OEM application in which Control Systems Engineers have devoted many years in development
Wind Energy
Being a renewable energy source in India There is lot of potential in this business. Power supply & Demand gaps provide more thrust in this business. Control Systems Engineers had Started the business in this sector from 1998 & all these Years developed the Control Panels / power Panels / pitch Panels / capacitor Panels& battery boxes. In conclusion in LT side of wind energy all the components for controls are developed, Produced in mass & running successfully at various site Conditions in India. Control Systems Engineers has supplied Panels for 350kw / 1 MW / 1.25 MW / 1.5 MW and battery boxes wind turbine generators. Panels manufactured for The hub are pitch Panel and battery boxes requires more precision as Panels are rotated 360 degree every day.
Compressor
Being a utility customer wants uninterrupted source of air/gas for the in-house use. Compressor Control Panels is manufactured with simplest from annunciator Panels To most complex like touch screen controls via PLC / MMI's. Panels provided for hazardous are requirement in gas group IIA / IIB & IIC. Pressurized Panels are made as per NFPA 496 standard ( type Z Purge ). Control Systems Engineers had developed complicated logics for the multiple compressor installation for the sequencing and for the common controls.
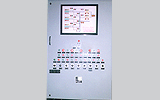 |
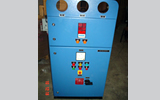 |
 |
Compressor Control Panel |
Compressor Control Panel |
Compressor Control Panel |
Flare Systems
In process plants flare system requires controls & monitoring of the ignitions & burners. Flare Panels are normally suitable for the hazardous are and have technology from relay based to more complicated PLC based.
Incinerators
For burning solid/ liquid wastes Control Panels required. Control Panel houses motor starters & instruments for the monitoring the systems. Desk type Panels are easy for the operator Interface/controls.
Evoporators
Evaporation is a process, which involves thermally removing the liquid from a solution, suspension or emulsion. The starting and end products are in the liquid phase and the end Product is obtained in the concentrated form. Evaporator control involves the speed control of conveyor, various interlocks for the drives and monitoring of the evaparator parameters.
Filtration systems
In the pharmaceutical industry the filtration is a phenomenon by which solid particles are removed from the liquid by means of process. Level monitoring and controls are provided in the processes. Speed of the motor is adjustable via variable speed drive to change the rate of the filtration. Various tripping interlocks are provided in the Panel for tripping and/or controlling the filtration process. Since pharma industry is a highly corrosive environment SS Panels are provided.
Boilers
For steam boilers & thermic fluid boilers Panels are provided for the controls and monitoring. All the operations are controlled via desk. Various process interlocks are taken care in the logic. To control the speed of the fuel feeder ac drives are provided. Drum level in the boiler is continuously monitored and controlled.
Chillers
Chillers are provided to cool the liquid in the continuous process plants. Chiller Panels require more & more automation and hence PLC / MMI provided for the applications.
Spray Driers
Spray drying is the transformation of feed from a fluid state into a dried particulate form by spraying feed into a hot drying medium.
Spray drying system consists of four process stages.
A) Atomization of feed into a spray.
B) Spray - Air contact
C) Drying of spray
D) Separation of dried product from the air.
The feed is pumped from the product feed tank to the Rotary Atomizer system which is located within a ceiling air disperser through which drying air enters the drying chamber. The air is drawn from atmosphere by a supply air blower and passed through an direct Hot Air Generator. As and when the drying air comes in contact with the spray, evaporation starts and dried powder particles falls to the base of the chamber. The exhaust air passed to the atmosphere via exhaust air blower and Wet scrubber. Adequate instrumentation is given for inlet temperature and outlet temperature, chamber pressure control, air damper controls for adjusting air flow rate and it will act as output of PID controller on a specified temperature depends on product properties. Vacuum levels are to monitored at various levels. Pressure transmitters are provided on feed line. Explosion control are provided as safety precaution. Alarm anounciator is provided for fault location. We supply MCC and instrument panel with rating and reputed make of electrical switch gears, instruments and accessories.
|